Lubricants
- florile
- Apr 3
- 5 min read
Summary
What are Lubricants?
Introduction
Industrial lubricants play a vital role in industrial maintenance, contributing significantly to operational efficiency, equipment lifespan and reduced maintenance costs.
The role of Industrial Lubricants is to reduce friction and wear: Industrial lubricants are formulated to create a protective layer between moving metal surfaces. This layer reduces friction and wear, improving efficiency and preventing premature component failure, in industrial processes, many machines generate heat due to friction and mechanical resistance.
Friction and viscosity
Friction is the resistance exerted between two surfaces in reciprocal motion. It can be reduced by interposing a fluid: the lubricant-coolant that avoids direct contact between the surfaces, constituting a system with a low friction coefficient.
The lubricant that separates the two metal parts constitutes a system of layers parallel to each other. Each layer of lubricant, however, opposes a certain resistance to the motion of the adjacent layer.
Viscosity is a quantity that varies significantly with temperature: as it increases, the viscosity of the lubricant decreases exponentially. To describe in a simple way the behavior of the viscosity of an oil with variations in temperature, a numerical parameter called "viscosity index" is used. The higher the viscosity index, the lower the variation in viscosity with variations in temperature.
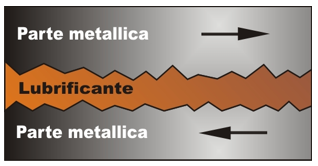
The composition of cooling lubricants
Lubricating oils are very complex products, made up of numerous components that can be divided into two general classes: base oils and additives. If the lubricating-cooling substance of an oil is a petroleum derivative, it will be said to be mineral oil-based, while lubricating-cooling substances derived from other chemical substances are synthetic oil-based.
Additives, meticulously inserted into the formulations of lubricating-cooling agents, are chemical substances that confer specific characteristics depending on the intended use of the lubricant. Additives can be: antifoams, corrosion inhibitors, friction modifiers, antioxidants, metal deactivators or viscosity index improvers.

The advantages of lubricants
Properties of Cooling Lubricants
As seen, cooling lubricants are divided into mineral-based oils and synthetic oils, a further classification can be made by dividing the cooling lubricants based on the processing: oils for guides, gears or guides and slides will be hydraulic oils; oils for metalworking are neat oils or emulsifiable oils.
The main properties that a hydraulic oil must have to ensure regular operation and duration in service are: cleanliness and anti-foaming power, adequate viscosity, a high pour point, anti-wear properties, considerable stability to oxidation and ease of air release, resistance to rust and greasiness.
The cutting operation in metalworking produces a considerable amount of heat, for this reason the cooling lubricant must, in addition to lubricating the surfaces and decreasing the friction index, cool the machinery in order to decrease wear and increase the useful life of the machinery. The task of the latter is therefore to remove said heat, once produced, as quickly as possible by means of a cooling flow that invests the piece and the tool. Depending on the operating conditions, the type of cutting operation, the material being worked and the type of tool, a cooling action may be more necessary than a lubricating one and vice versa.

Whole cutting oils
Neat cutting oils are used as is. Their task is to be placed between the contact surfaces between the tool, the chip and the workpiece to reduce friction, i.e. the lubricating action. They prevent possible welding between the metal parts and at the same time remove the heat generated by the machining. Neat cutting oils are mainly made of mineral oils to which lubricating additives and/or additives are added.
Emulsifiable cutting oils
Emulsifiable cutting oils are used mixed with water at a percentage between 4 and 10% depending on the difficulty of the process. They perform a lubricating, anti-welding and significantly cooling action. Since they are mixed with water, they must have exceptional anti-rust and antibacterial power.
Emulsions are dispersions resulting from the mixing of two immiscible liquids: one of the two liquids constitutes the dispersed phase and is distributed in the form of droplets in the carrier liquid.
To prepare a lubricating-cooling emulsion, a concentrate consisting of mineral oil or synthetic oil, emulsifiers, corrosion inhibitor additives, lubrication improvers, anti-wear additives, anti-foam agents and biocides is used. The latter combat the attack on the emulsion by microorganisms that can contaminate the emulsion.

Management of coolants
Mixing must take place at room temperature. Adding the concentrated emulsifiable oil to the water, never vice versa; in the prescribed percentage, stirring regularly.
Water is the main component of coolant emulsions, its quality influences the stability and characteristics of the emulsions. The hardness of the water is the main characteristic of the water intended for the preparation of the emulsion. Water that is too hard damages the stability of the emulsion because calcium soaps insoluble in water are formed, white or yellowish in color, which separate from the emulsion and rise to the surface, giving rise to a layer of cream. On the contrary, water that is too soft gives rise to the formation of foam.
For these reasons, specific additives are inserted into the formulations to optimize the coolant based on the specifications of each customer.
Problems and remedies
Given the great experience FIPROKIM SRL has in the sector of coolants, over the years it has built up a know-how that allows it to manage any unexpected event thanks to its high problem-solving capacity.
Some examples of real problems encountered with the use of emulsifiable coolants are:
Difficulty in forming the emulsion, caused by storage errors or errors in preparation.
Unstable emulsion or breakage, caused by errors in preparation or contamination.
Appearance of rust, caused by unsuitable emulsion, inadequate concentration or contamination.
Appearance of foam, caused by inadequate filtration or inadequate concentration.
Wear of the tool, caused by inadequate concentration or inadequate filtration.
Problems in cleaning the circuit, caused by bacterial contamination in which total disinfestation and restoration is required.
Unpleasant odor, caused by a lowering of the pH value and bacterial contamination, until the emulsion breaks and needs to be restored.
Operator allergies, caused by bacterial contamination or external contaminants since there is no sensitizing substance in the formulations.
FIPROKIM lubricants

The LUBROFIP and OILPROT line
FIPROKIM SRL produces both mineral and synthetic oils, these can be whole or emulsifiable.
The LUBROFIP line includes all the lubricating-cooling oils and takes a specific numbering for each class: the whole mineral oils are LUBROFIP 5000, the whole vegetable oils are LUBROFIP 5500, the whole industrial oils are LUBROFIP 8000. The emulsifiable oils are divided into mineral-based emulsifiable oils LUBROFIP 4000, synthetic-based emulsifiable oils LUBROFIP 4500 and soluble emulsifiable oils LUBROFIP 4800.
Finally, there are particular oils specific for the protection between processing phases or for storage in an internal or external warehouse, the family of specific products is OILPROT.
These are the main FIPROKIM SRL lubricating and cooling products:
LUBROFIP 5000 LINE
Line of neat oils for metalworking. Suitable for cutting, chip removal, lapping, drilling, deep drilling, broaching, stamping, forming, drawing, metal wire drawing.
LUBROFIP 5500 LINE
Line of whole oils for metalworking based on renewable and vegetable sources. Suitable for cutting, chip removal, lapping, drilling, deep drilling, broaching, stamping, forming, drawing, metal wire drawing.
LUBROFIP 8000 LINE
The LUBROFIP 8000 industrial lubricant line is composed of oils for the operation of machine tools: hydraulic circuits, slide guides, compressors, gears, bar pushers, spindles.
LUBROFIP 4000 LINE
Emulsifiable based on highly refined mineral oil with appropriate additives for all mechanical cutting, grinding and moulding processes.
LUBROFIP 4500 LINE
Emulsifiables based on synthetic esters derived from plant and renewable sources appropriately added for all mechanical cutting, grinding and moulding processes.
LUBROFIP 4800 LINE
Line of soluble products, free from oil.
In water they form a clear solution suitable for grinding and medium-heavy mechanical processing.
OILPROT LINE
Metal protectors suitable for protecting worked metal from oxidation for long periods of time.

CHEMICALS PRODUTCS